|
Part Two: Building the Trestle Base
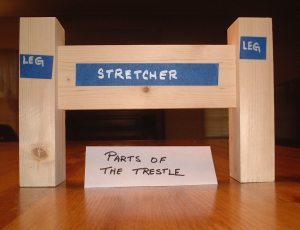
While the glue dries, I’ll set the top aside and work on the base.
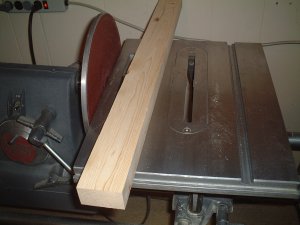
I had a bad spot on the edge of this board, but it only took a couple of seconds to clean it up with the disk sander. Looks great now, doesn’t it?
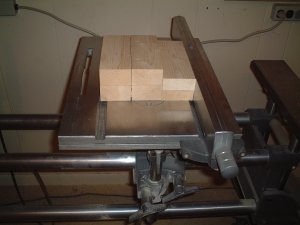
After a little more work at the table saw I’ve got all of the boards I need to make the trestles.
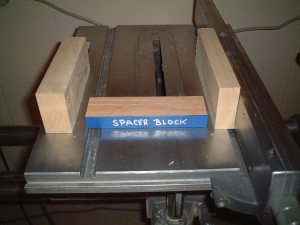
This is where the Shopsmtih has it over other machines. Assembly of the trestles takes place right at the Shopsmith. I’ll drill holes (using then Shopsmith in horizontal boring mode) and then put in screws while everything is still clamped and lined up. It virtually guarantees that everything will be square.
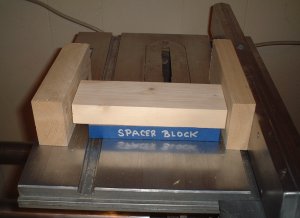
Rather than spend a lot of time mindlessly measuring, I’m using spacer blocks. These are just scraps of wood that I have around the shop.
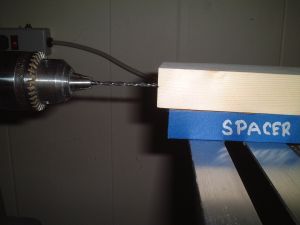
Before I get everything set up, I want to make sure that I’ll be drilling near the center of the board. Again, no measuring—I’m just eyeballing this. Once I lock the table height, I know that all my holes will line up and they will be the exact same distance from the bottom of the leg—without measuring!
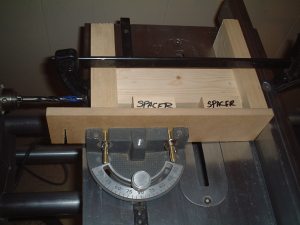
A couple more spacer blocks determine the distance for the stretcher bar. Notice how I’m using the miter gauge and rip fence to keep things square. A single clamp holds things in place.
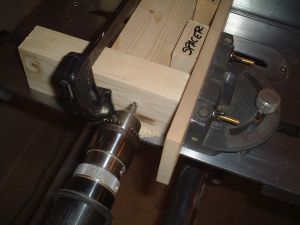
I’m drilling the pilot holes and counterbores before changing the setup. I don’t have stepped bit, so I just swap bits, drilling the larger hole first. Due to the precision of the Shopsmith, I can change bits and drill the second hole right on center with the first.
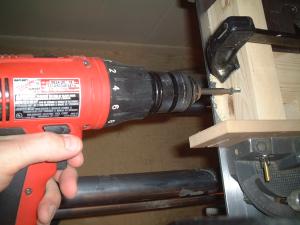
With everything still clamped in place, I pull the headstock back and screw the pieces together. Because I haven’t changed the setup, I know the pieces will be lined up and square as I screw them together.
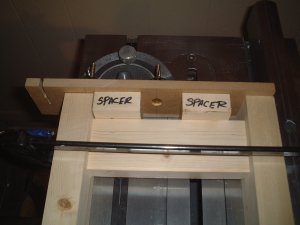
I’m repeating the same operation on the other side of the trestle so the setup is slightly different.
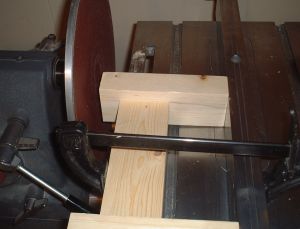
The ends of the boards will be visible, so I’m using the disk sander to smooth things out. It’s almost the same setup as the drilling operation, so I’m doing the sanding now.
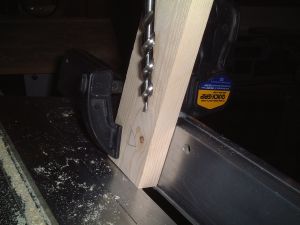 Screws set in angled pocket holes will hold the stretcher in place. The easiest way to drill these is with the Shopsmith set up as a vertical drill press. The table is tilted about 15 degrees off vertical, which creates an angled hole. The bit I am using is from a Kreg jig, and you can get it (the bit, not the jig) for about fifteen bucks at a home center near you. You could also use a Forstner bit for the large part of the hole and a brad point bit for the narrow part.
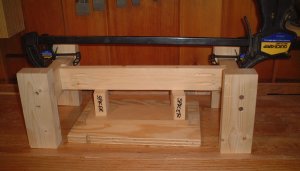
Once again, I am using spacer boards and a clamp to hold things together while I fasten the screws.
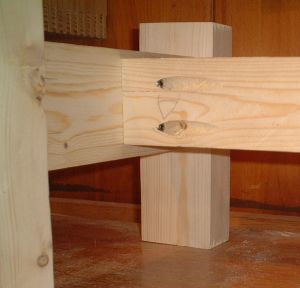
The pocket holes work well, but they sure are ugly.
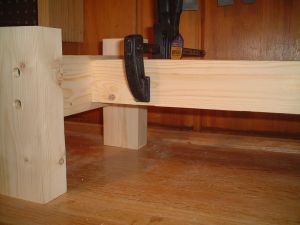
I’m gluing on a half inch layer of wood to hide the pocket holes and make it look like I used a blind mortise-and-tenon joint.

|